Sina Ekato, a renowned manufacturer in the field of stainless steel storage tank production, has gained significant recognition for its expertise and commitment to quality. With a focus on catering to customer needs, Sina Ekato offers custom capacity options, providing clients with tailored solutions for their storage requirements.
Stainless steel storage tanks are widely used in food and beverage, pharmaceutical, daily chemical, water treatment and other industries. They are an important asset, ensuring the safe and efficient storage of various substances. One of the main advantages of stainless steel storage tanks is their durability and corrosion resistance, making them suitable for storing large amounts of liquid or gaseous materials.
Sina Ekato’s production process for custom capacity stainless steel storage tanks follows industry-leading practices. The company employs a team of highly skilled engineers and technicians who possess extensive knowledge and experience in designing and manufacturing storage tanks. With a strong focus on quality control, Sina Ekato ensures that its tanks meet all relevant industry standards and regulations
When it comes to custom capacity stainless steel storage tank production, Sina Ekato offers a range of options to meet individual specifications. Our company understands that cosmetics industry applications have unique storage needs. By providing customized capacity solutions, customers can ensure that they receive tanks that precisely match their needs, resulting in increased efficiency and productivity.
Sina Ekato’s commitment to customer satisfaction and their ability to deliver high-quality custom capacity stainless steel storage tanks has earned them an impeccable reputation in the industry. Clients appreciate the company’s attention to detail, reliable performance, and ability to meet deadlines. Whether it’s a small-scale project or a large-scale industrial undertaking, Sina Ekato possesses the expertise and resources to fulfill diverse customer demands.
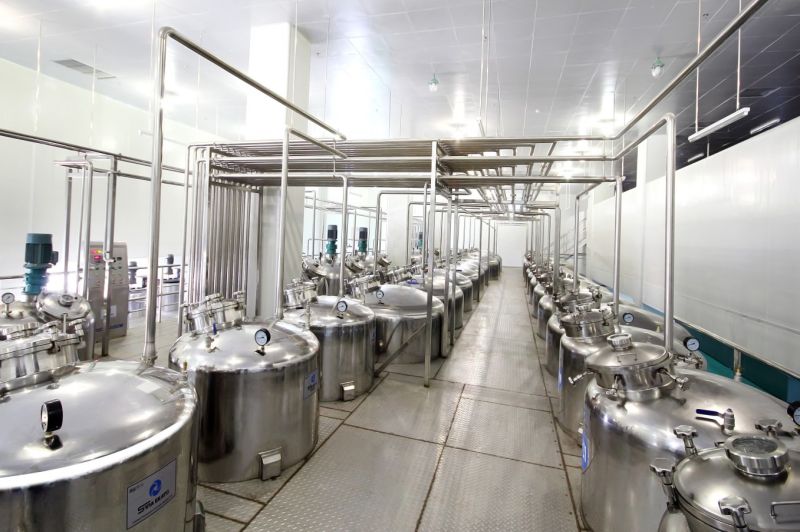
In conclusion, Sina Ekato takes pride in its custom capacity stainless steel storage tank production. By offering tailored solutions, the company ensures that its clients can benefit from storage tanks that precisely meet their specifications. With a strong emphasis on quality and customer satisfaction, Sina Ekato continues to establish itself as a leader in the field of stainless steel storage tank production.
Stainless steel storage tank production involves a series of steps to manufacture high-quality tanks suitable for various applications. Here is a general overview of the production process:
1.Design and Engineering: The first step is to design the storage tank based on the specific requirements and constraints. Engineers use computer-aided design (CAD) software to create detailed drawings and specifications.
2.Material Selection: Stainless steel is the preferred material for storage tanks due to its inherent corrosion resistance and durability. The specific grade and thickness of stainless steel are selected based on the tank’s intended use and the stored substance.
3.Material Preparation: The stainless steel sheets are cut according to the predetermined dimensions for various tank components such as shell, bottom, and roof. Cutting methods such as laser cutting, plasma cutting, or shearing are employed for precision.
4.Welding: The components are then welded together to form the tank structure. Various welding techniques, such as TIG (tungsten inert gas) welding or MIG (metal inert gas) welding, are used to create strong and leak-proof joints. Care is taken to ensure proper weld penetration and metal deposition to maintain the tank’s integrity.
5.Surface Treatment: The welded tank undergoes surface treatment processes to remove any impurities, such as welding slag or oxide layers. Processes like grinding, passivation, or pickling are employed to achieve a smooth, clean surface finish and improve corrosion resistance.
6.Quality Control: Throughout the production process, rigorous quality control measures are implemented to ensure the tanks meet industry standards and customer specifications. Non-destructive testing techniques, such as ultrasonic testing or radiographic inspection, are employed to detect any structural defects or imperfections.
7.Final Assembly: Once the tank structure is complete, additional components like nozzles, manholes, support legs, and access platforms are installed as per design requirements. Piping systems, valves, and instrumentation may also be integrated into the tank assembly.
8.Testing and Certification: The finished stainless steel storage tanks are subjected to hydrostatic testing, where they are filled with water or another suitable fluid to check for any leaks or structural weaknesses. Certifications and compliance documents are issued to ensure the tanks meet relevant industry standards and codes.
9.Delivery and Installation: The completed tanks are then packaged and transported to the site for installation. Adequate logistics and handling procedures are followed to prevent damage during transit. Upon reaching the installation site, the tanks are carefully positioned, levelled, and connected to the required utilities.
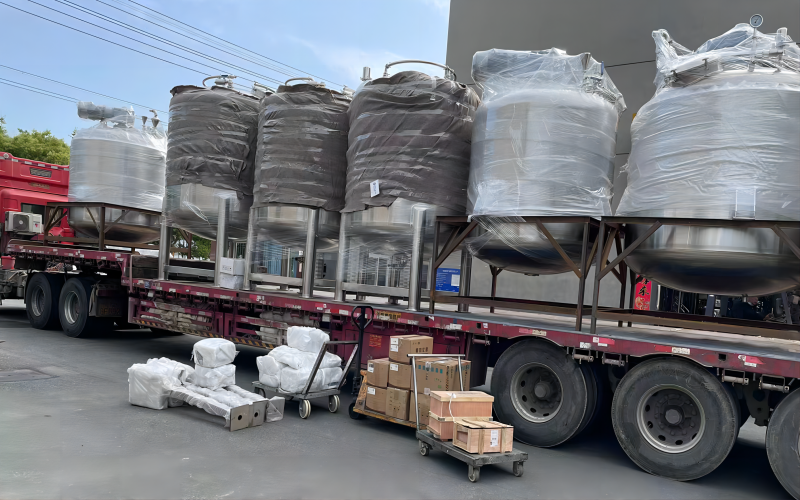
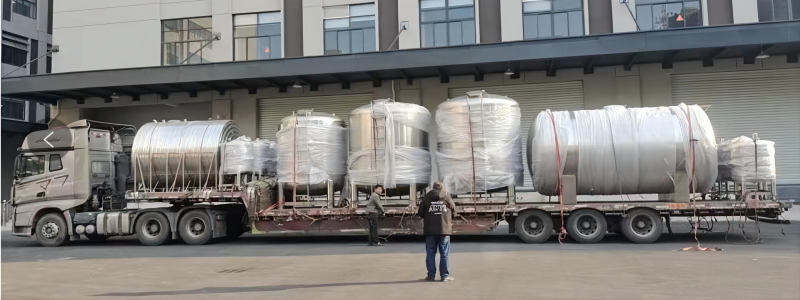
It is important to note that the production process may vary depending on factors such as tank size, operating conditions, and customization requirements.