Description
Application
Daily cosmetic |
|||
hair conditioner | facial mask | moisturizing lotion | suncream |
skin care | shea butter | body lotion | sunscreen cream |
cream | hair cream | cosmetic paste | BB Cream |
lotion | face wash liquid | mascara | foundation |
hair color | face cream | eye serum | hair gel |
hair dye | lip balm | serum | lip gloss |
emulsion | lipstick | highly viscous product | shampoo |
cosmetic toner | hand cream | shaving cream | moisturizing cream |
Food & Pharmaceutical |
|||
cheese | milk butter | ointment | ketchup |
mustard | peanut butter | mayonnaise | wasabi |
toothpaste | margarine | Salad dressing | sauce |
Performances And Features
1. Bottom Homogenizer & external circulation homogeneous System. The bottom of the emulsifying pot is homogenized, and the material can be recycled through the circulating pipeline, and constantly repeated through the mixing and the shear mixing of the homogenizer, to achieve a fast and efficient dispersion, emulsification, mixing, uniform mixing effect.
2. The vacuum emulsifying mixer with a helical ribbon mixing and double-way mixing system is designed to ensure even mixing and emulsification of ingredients. The helical ribbon mixing system consists of a helical ribbon agitator that rotates inside the mixing vessel. This agitator has a helical shape, which helps to efficiently move and mix the ingredients. As the helical ribbon rotates, it creates a gentle kneading and folding action, ensuring thorough blending of the ingredients. The double-way mixing system, on the other hand, involves the use of two mixing directions. This system utilizes multiple mixing blades that move in opposite directions, further enhancing the mixing efficiency. The dual mixing action helps to create a more uniform dispersion of ingredients and ensures that all components are evenly distributed throughout the mixture.
3. The vacuum homogenizer emulsifying mixer with Siemens inverter frequency conversion speed regulation The variable speed control allows the operator to adjust the mixing speed according to the specific requirements of the process. This feature is particularly useful for applications that require different mixing speeds at different stages or for different types of materials. By adjusting the speed, the operator can optimize the mixing process and ensure efficient and effective emulsification. The Siemens inverter frequency conversion speed regulation is a technology that provides precise and stable speed control. It allows for seamless speed adjustments, ensuring smooth operation without sudden changes in speed that could impact the quality of the mixture.
4. Aseptic processing: The vacuum homogenizing emulsifier is equipped with a high-precision temperature and pressure control system, which can realize aseptic processing and meet the requirements of the food and pharmaceutical industries.
5. The lifting systems double-cylinder lifting. By having a double-cylinder lifting system, the vacuum emulsifying machine becomes more versatile and customizable, catering to different manufacturing needs and processes. It enhances batch-to-batch consistency and allows for better control over the emulsifying process, resulting in more uniform and high-quality products.
6.The master pot dumping system is used to dump material from the master pot of the vacuum emulsifier into downstream equipment or containers. It consists of a tipping device and a control system. The tipping device usually uses a hydraulic mechanism that tilts the main pan to dump the material. The control system can be controlled by a touch-screen PLC to easily control the dumping process.
7. The maximum emulsifying rotation speed can reach 3500 rpm and the highest shearing fineness can reach 0.2-5 um. The vacuum defoaming can make the materials meet the requirement of being aseptic.
8. The vacuum material sucking is adopted, and especially for the powder materials, vacuum sucking can avoid dust. The emulsifying pot lid can adopt lifting system, easy to clean and the cleaning effect is more obvious, the emulsifying pot can adopt tilt discharge.
9. The pot body is welded by imported three-layer stainless steel plate. The tank body and the pipes adopt mirror polishing, which fully conforms to GMP requirements. According to technological requirements, the tank body can heat or cool the materials. The heating modes mainly include steam heating or electric heating. To ensure the control of the whole machine is more stable, the electric appliances adopt imported configurations, so as to fully meet the international standards.
10.The CIP(Clean in Place) system is a key component of this vacuum emulsion mixer, ensuring efficient cleaning and hygiene after each batch of equipment. It is designed to simplify the cleaning process, save time and minimize manual labor. CIP systems for vacuum emulsion mixers include the following features: Spray balls or nozzles: These are strategically placed in the mixing vessel. Spray a cleaning solution or water under pressure to cover all surfaces evenly. Recirculation pump: The CIP system contains a recirculation pump that circulates the cleaning solution through a spray ball or nozzle. This ensures uniform distribution and thorough cleaning of all parts of the vacuum emulsifying mixer. Control system: The CIP system is controlled by a user-friendly control panel that allows the operator to set cleaning parameters
Technical Parameter
Model | Capacity | Homogenizer Motor | Stir Motor | Dimension | Total Power | Limit vacuum(Mpa) | |||||
KW | r/min | KW | r/min | Length(mm) | Width(mm) | Height(mm) | Steam heating | Electric heating | |||
SME-1000 | 1000L | 15 | 0-3000 | 5.5 | 0-63 | 4200 | 3650 | 3300 | 30 | 90 | -0.08 |
Note: In case of inconformity of the data in the table due to technical improvement or customization, the real object shall prevail |
Product Details
Note: The picture is customized for reference only
- ◇Sealed manhole: convenient to clean and maintain. ◇Glass view window : check inside working situiation. ◇Essence inlet: add powder ◇Production inlet: Suck products into working pot in vacuum condition. ◇Air filter: filter aire and prevent dust into working pot ◇Pressure gauge: shows the pressure of working pot ◇CIP system inlet: equip with CIP spray ball to clean inside tank and mixing paddle.
- Mixing paddle ◇Frame mixer: frequency speed adjustment, 0-63rpm ◇Fixed paddle : avoid the big vortex during mixing process ◇Teflon scraper: high temperature resitance, wearproof, food grade。 ◇Homogenizer mixer: High shear emulsifier mixer, 0-2880rpm ◇CIP system: 360 degrees rotate to spray water to clean inside. ◇Temperaure probe : detect the temperature of products
- Vacuum pump and heating system ◇Water seal vacuum pump: connect tap water before sucking vacuum. ◇Electric heating rod : Jacket water inlet connect with tap water to heat or cool products.
- Control panel ◇Function: Heating, mixing, emulsifying, ◇Setting : Heating temperature, mixing speed, homogenizer speed, homogenizer time
- Siemens touch screen operating system
- Convenient electric control button
- Discharge outlet◇Butterfly valve: ◇Stainless steel outlet pipe SUS316L ◇Also can adopt a pump to dicharge product rapidly.
- Oil Pot-Water Pot Pre-treatment System Water phase andoil phase pot to pre-heat and dispersethe raw materials, then transfer them tomain pot to begin production.
Relevant Machines
We can offer machines for you as following
Reverse osmosis water purifier, vacuum homogenizing emulsifier. aseptic storage tank, drying sterilizer, ointment filling machine. conveying workbench, code printer, labeling machine, aluminum foil sealing machine, shrink film machine
Click the picture to jump to the link related to the product
- RO Water Machine
- Bottle Washing Machine
- Bottle Drying Sterilizer
- Stainless steel storage tank
- Cream & Paste Filling Machine
- Splint type sachet packing machine
- Tube Filling And Sealing Machine
- Automatic aluminum foil sealing machine
- Labelling Machine
- Automatic Capling Machine
Company Profile
With the solid backing of jiang su Province gao you city Xinlang Light
Industry Machinery & Equipment Factory, under the support of German design center and national light industry and daily chemicals research institute, and regarding senior engineers and experts as the technological core, Guangzhou SINAEKAT chemical Machinery Co, Ltd. is a professional manufacturer of various types of cosmetic machinery and equjpment and has become a brand enterprise in the daily chemical machinery industry. The products are applied in such industries as. cosmetics, medicine, foodchemical industry, electronics, etc., serving many nationally and internationally famous enterprises suchas Guangzhou Houdy Group, Bawang Group, Shenzhen Lanting Technology Co., ltd, Liangmianzhen GroupZhoneshan Perfect, Zhoneshan Jial, Guanedone Yanor, Guanedone Lafane. Beine Dabao, Japan Shiseidokorea charmzone, France shiting, Usa JB, etc.
Workshop Production
Our Advantage
With many years of experience in domestic and international installation, SINAEKATO has successively undertaken the integral installation of hundreds of large-sized projects.
Our company provides internationally top-ranking professional project installation experience and management experience.
Our after-sales service personnel have practical experience in equipment use and maintenance and receive systemic trainings.
We are sincerely providing customers from home and abroad with machinery & equipment, cosmetic raw materials, packing materials, technical consultation and other service.
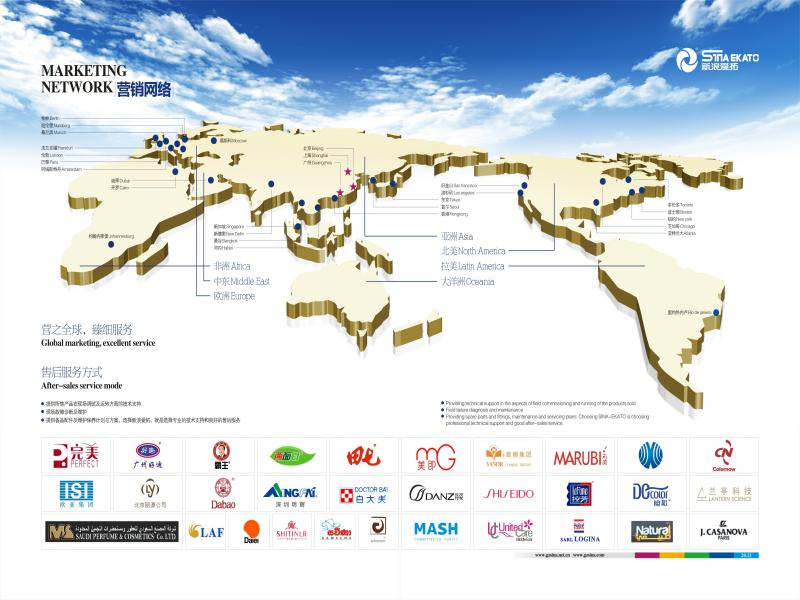
Our Project
Packing and Shipping
Exhibitions & Customers visit factory
Cooperative Customers
Material Certificate
Contact Person
Ms Jessie Ji
Mobile/what’s app/wechat: +86 13660738457
Email: 012usinaekato.com
official website: http://www.sinaekato.group
Reviews
There are no reviews yet.